Prep Pro 6000 Prep Station
The Prep Pro 6000 design is the widest prep station we make! This 76 inch wide ductless prep station is the one that you need when LARGE is what you are looking for. Almost as wide as a full size spray booth, this model has it all. Simple to operate and maintain, and can be moved anywhere you need it.
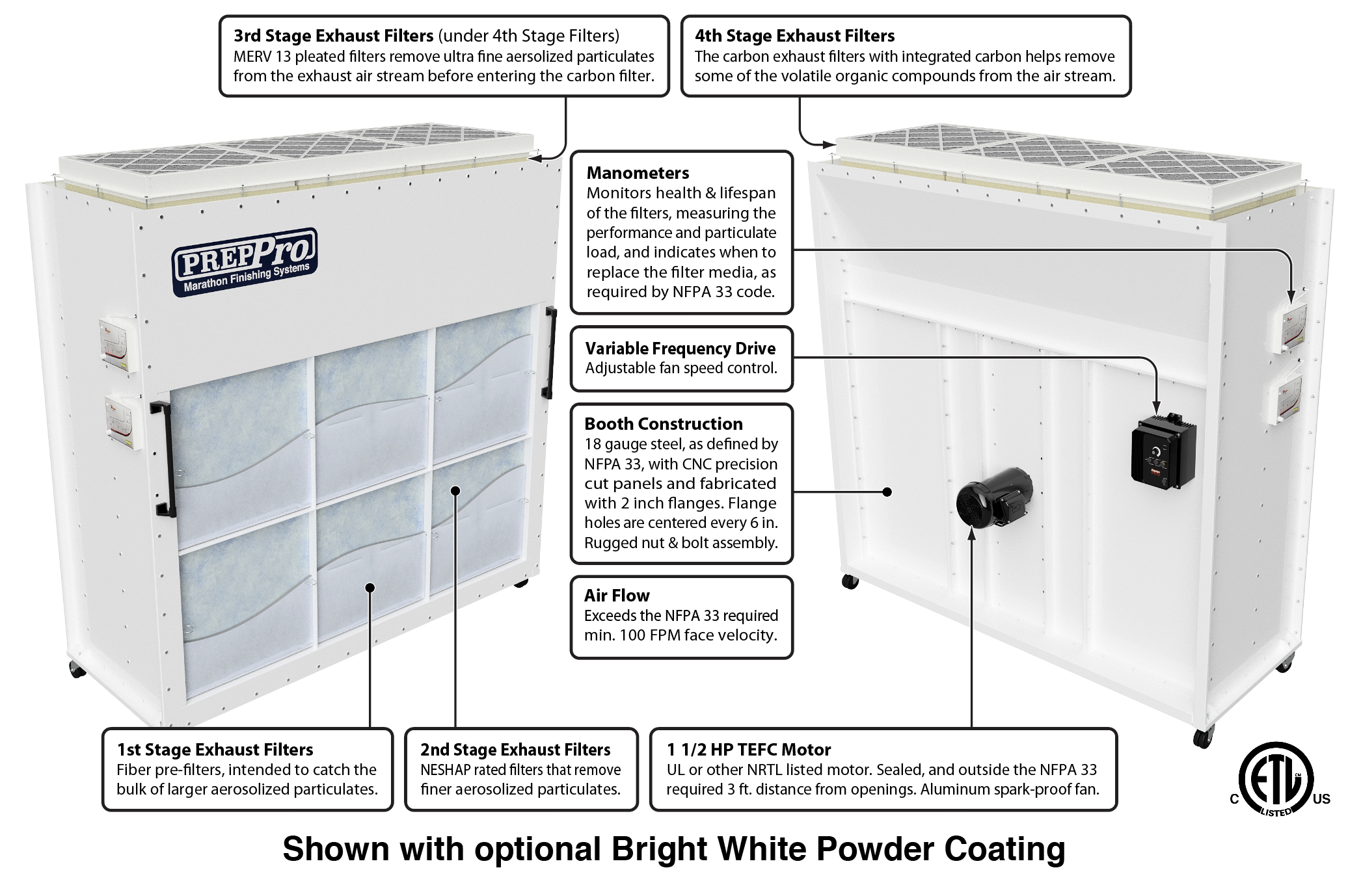
Did you Know?
The ETL Listing (certification) is your confirmation that every aspect of our construction meets or exceeds the build and safety code standards established by NFPA 33. This is important, as your Fire Inspector will require proof of compliance before approval.
Our Certifications
The ETL Listed Mark (shown below) indicates that Marathon Finishing products have been evaluated and tested by InterTek, a Nationally Recognized Testing Laboratory (NRTL) and have been found to meet or exceed all required national safety standards for the US and Canada.
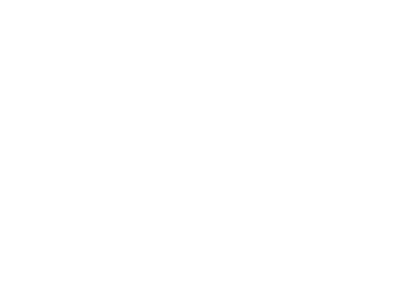
Our Standards
All of our products meet or exceed the following national safety and fire standards:
- International Fire Code (IFC)
- California Fire Code (CFC)
- National Fire Protection Assn. Code 1 (NFPA 1)
- National Fire Protection Assn. Code 33 (NFPA 33)
- National Fire Protection Assn. Code 70 (NFPA 70)
- International Mechanical Code (IMC)
- Occupational Safety Hazards Assn. (OSHA)
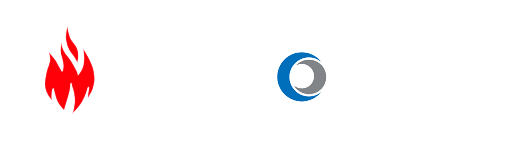
The Prep Pro surface prep stations are the best products of their type available anywhere. We use the exact same materials and design techniques that we use on our large full size spray paint booths when making the prep pro models. The housing is made from 18 gauge steel CNC precision cut with holes every 6″ on center with full 2″ companion flanges. Assembled using rugged nuts & bolts, not zip screws!
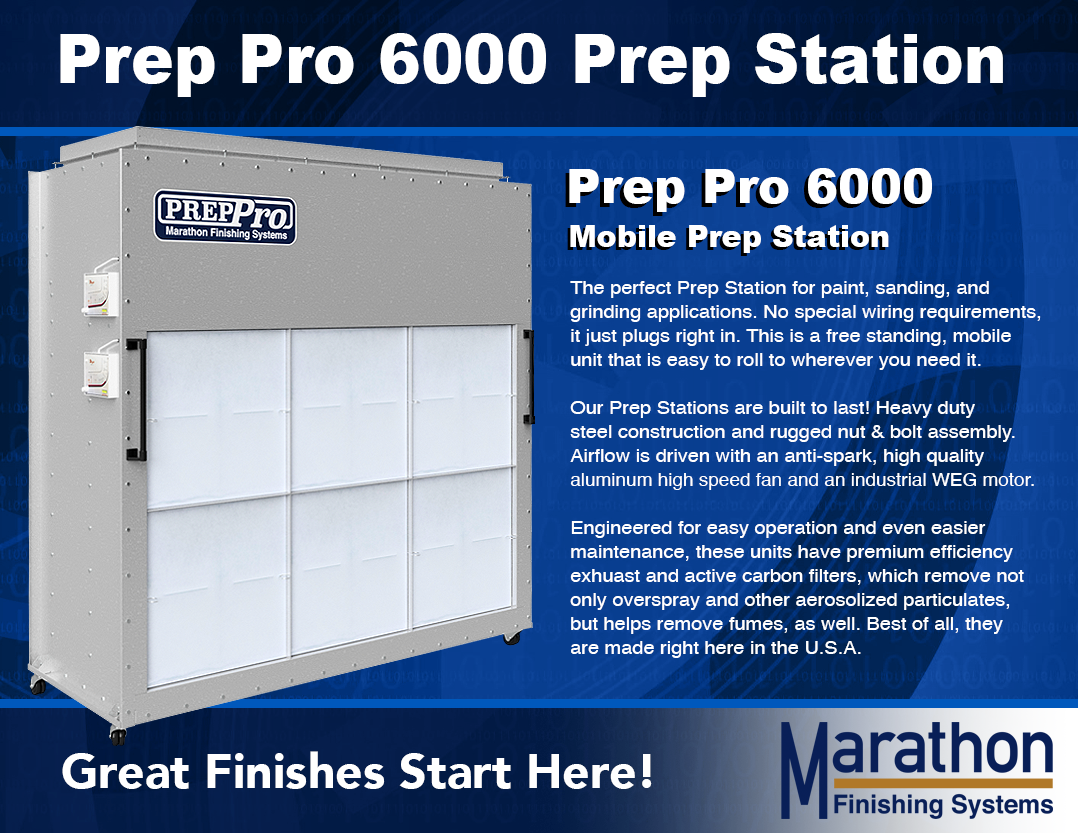
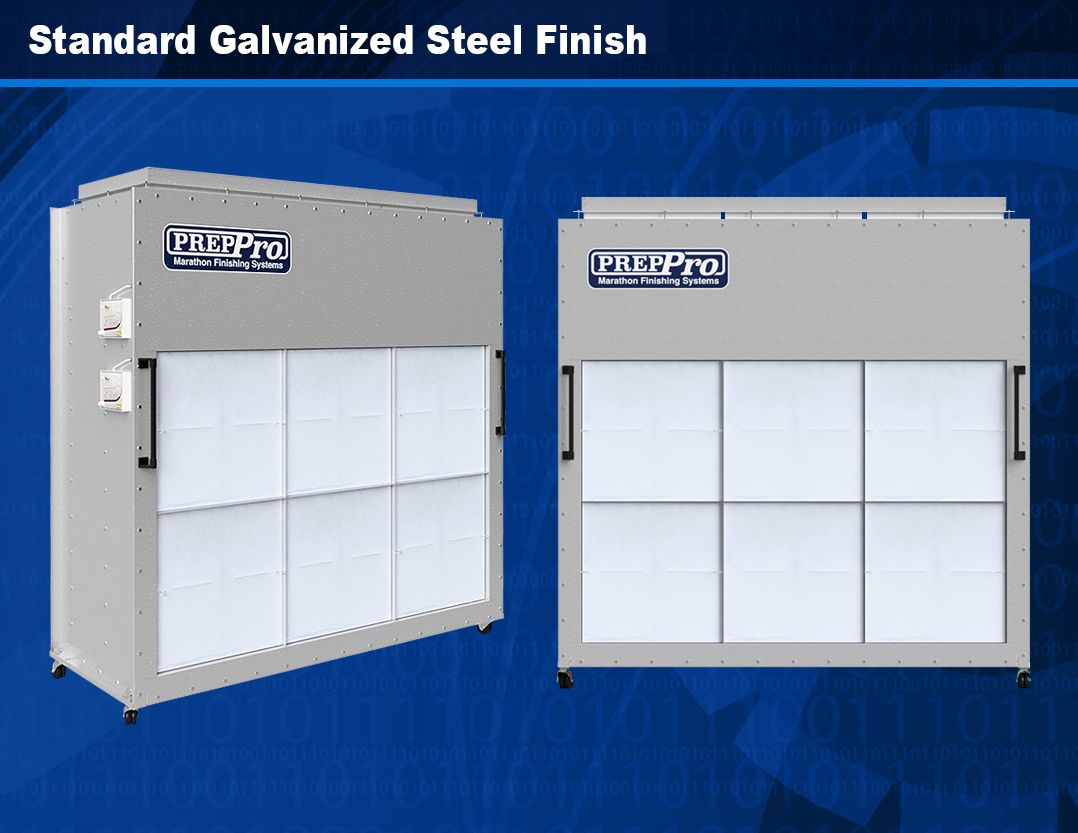
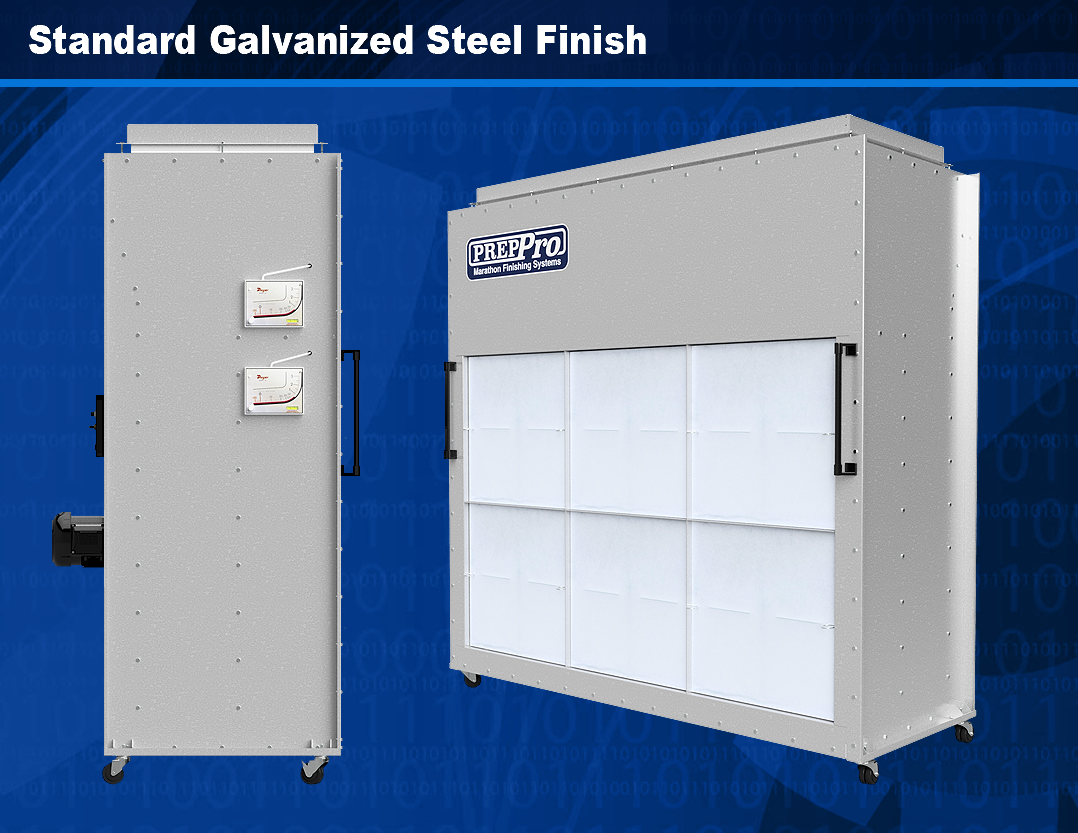
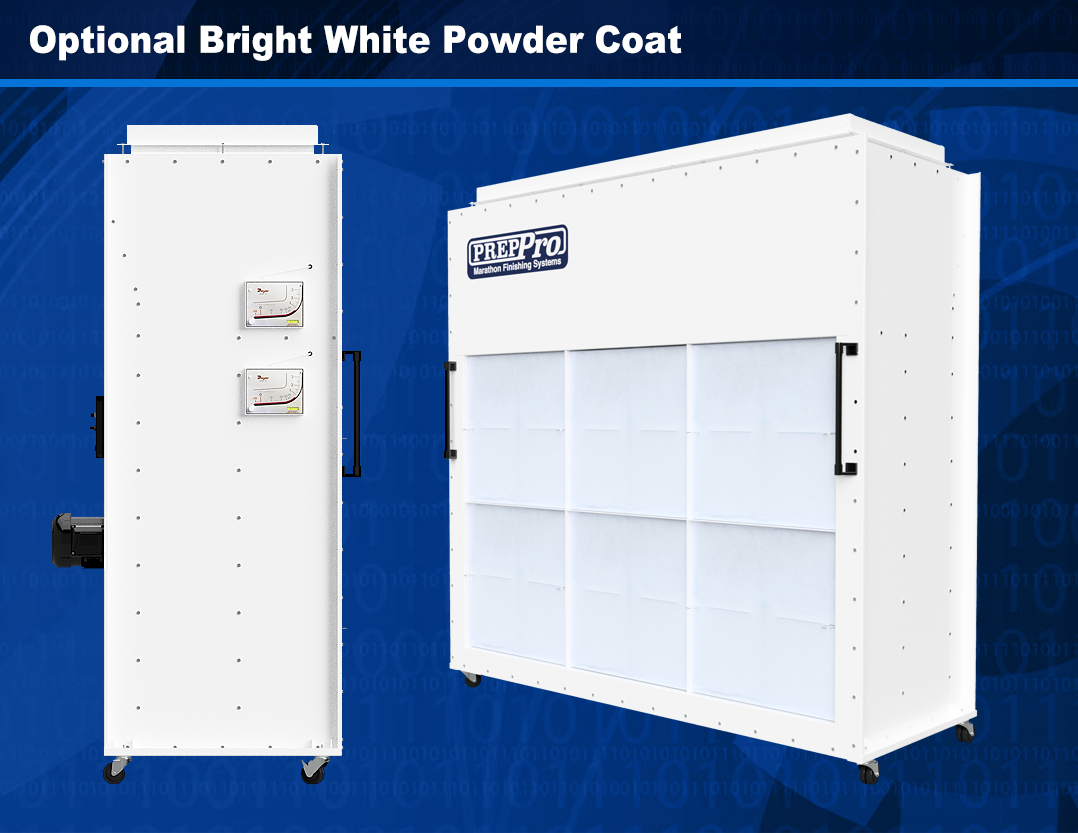
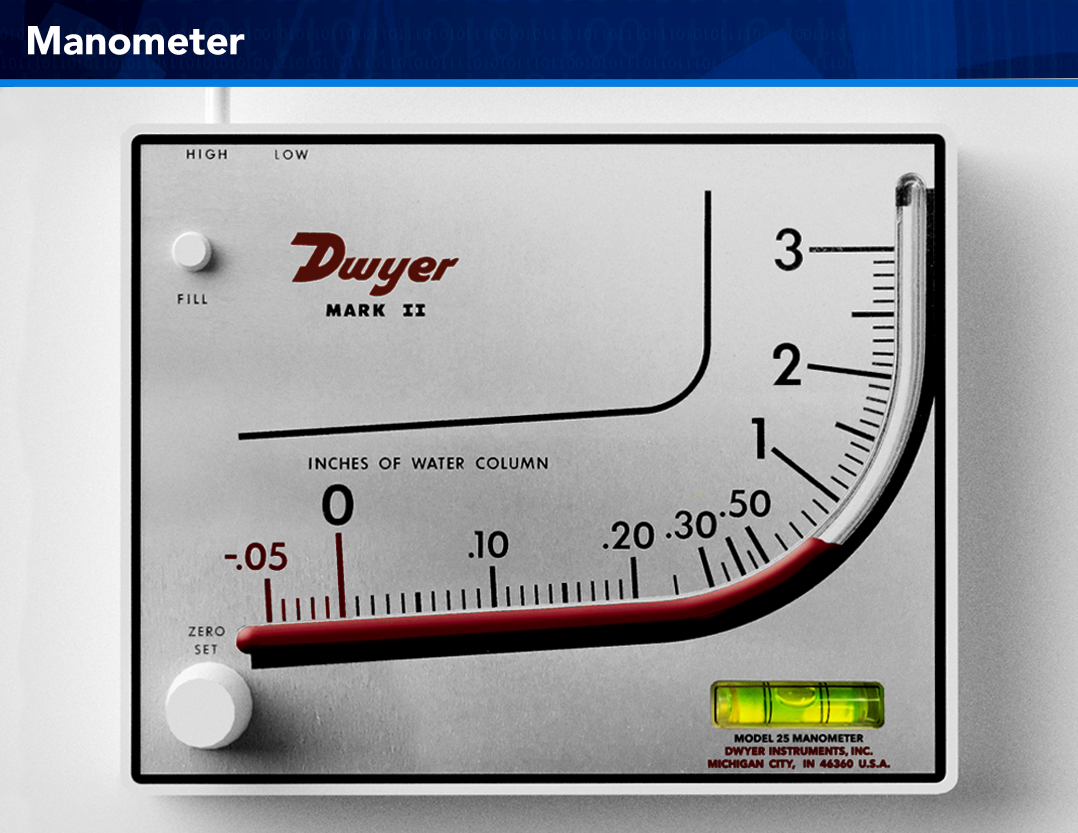
Call us at 951-327-7503 and tell us which of these options you are interested in. You’ll see why we say Marathon Finishing is the Benchmark for spray painting solutions!